Couplings
Dalatec Corporation works directly as a sales facility/integrator with several coupling manufacturers.
A coupling is a device used to connect two shafts together at their ends for the basic function of transmitting power, and to accommodate misalignment as well as compensate for axial movement (end movement of shafts).
Selecting the right coupling depends on four basic conditions of the shaft misalignment or movement.
- Parallel misalignment: two shafts may have their ends facing parallel but their center axes are laterally displaced with respect to each other. This occurs when the two shafts do not share the same rotation axis. Their ends face may be parallel, but their center axes are laterally displaced with respect to each other.
- Angular Alignment: Angle can be misaligned symmetrically or asymmetrically. This applies when shafts are neither coaxial nor parallel.
- Torsional flexibility: This is the torsional movement in planes perpendicular to the shaft axis. Shock or vibration typically causes this. A torsionally flexible coupling absorbs and dampens these movements.
- End float: This occurs when either or both shafts display axial movement, moving in and out. A sleeve-bearing motor, for example, "floats" as the rotor hunts for the magnetic center of the winding. Temperature variation can also cause thermal expansion and variation in position of the shafts.

Below is a list of some of the Companies we work with for your coupling needs:
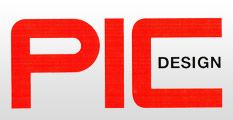
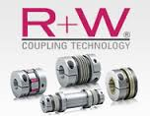
Over 150 employees
Branch offices located in the United States, China, France, Switzerland and Italy
Over 60 representatives worldwide
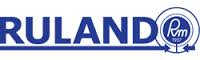
Ruland started business in 1937 and specialize in Shaft collars and couplings manufacturing.
Ruland manufactures shaft collars in multiple styles to fit shafts ranging from 1/8" to 6" in the inch series and 3mm to 150mm in the metric series. Ruland shaft collars are available in a variety of materials and finishes including: 303 & 316 stainless steel, black oxide and yellow zinc plated carbon steel, high-strength aluminum, and engineered plastic. Each shaft collar is stamped with the Ruland name and bore size for easy identification.
Extra steps are taken in the manufacture of Ruland shaft collars to provide important performance benefits. For example, they are single point faced (indicated by the circular groove on the face) during the boring operation to insure perpendicularity of the face to the bore. This results in a face runout of TIR ≤ .002" (.05mm) on standard shaft collars with even tighter tolerances on bearing lock-nuts and special designs. Perpendicularity is important for alignment when a shaft collar is used as a load-bearing face, mechanical stop, or for mounting components such as gears or bearings.

One-piece shaft collars wrap around the shaft for even distribution of clamping forces. This results in a tight fit and greater holding power, without the shaft damage caused by set screws. Clamp collars are easy to remove, indefinitely adjustable, and work well on virtually any shaft. Ruland uses carefully selected materials and proprietary processes on its one-piece collars to ensure the clamping gap remains open for simpler and more precise adjustment, installation and fit.
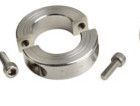
Two-piece shaft collars offer the same benefits as one-piece shaft collars with additional versatility and convenience. The split design is easily installed and disassembled, reducing labor and downtime when adjustment, removal, or replacement is necessary. The two-piece shaft collar uses the full seating torque of its forged screws to apply a uniform distribution of forces around the shaft's circumference. These clamping forces provide the collar with a holding power superior to one-piece and set screw shaft collars. Ruland keeps both halves of the split collar together throughout the manufacturing process to assure a perfect match for proper fit, alignment, and holding power. This process also makes the two-piece collar more adaptable to shafts which vary a small amount from nominal size.

Threaded shaft collars and bearing lock-nuts share the same quality and benefits of their smooth bore counterparts, while providing additional features. Threaded collars provide axial holding power which is superior to smooth bore collars, while offering easier installation and adjustment than solid ring locking devices. A diverse list of thread sizes and pitches, including locknut threads, are offered. Ruland double taps each threaded collar and bearing lock nut to insure precise and burr-free threads to allow for easy installation and removal, proper fit, and extended shaft life.

Set screw shaft collars are the most effective when used on a shaft made of a material which is softer than the set screw. Ruland set collars are furnished exclusively with forged socket set screws for greater torque capacity and improved holding power. Forging of the stainless steel set screws has the additional benefit of work hardening, which results in stainless steel with elevated hardness and performance.
International series shaft collars are offered in one and two-piece styles and feature inch bores with metric outer diameters, widths and DIN 12.9 socket headed cap screws. The use of metric screws with inch bores is especially useful when either retrofitting or designing equipment with inch shafts for worldwide use. The International series shaft collar is available in bore sizes from ¼" to 3" with outside diameters from 18mm to 108mm.
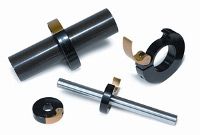
Quick-clamping shaft collars are ideal for light duty or low-rpm applications that require frequent setup changes or adjustments. The handle sits flush with the outside diameter allowing the shaft collar to be precisely adjusted by hand without the need for tools. The quick-clamp shaft collar is made from aluminum and has a black anodized finish with stainless steel hardware. They do not mar the shaft.
Thin line shaft collars are designed for applications with space and weight restrictions in industries such as packaging, printing, medical, and food, and are particularly suitable for split hub componentry such as encoders. They function as clamps, positioners, guides, spacers, and stops in a smaller profile than traditional shaft collars. Two-piece styles have a balanced design for higher RPM applications. Most bore sizes are available with different outer diameter and width dimensions and screw sizes allowing the user to match space limitations and holding power with their application requirements. Hygienic clamping assemblies are ideal for high pressure wash down applications found in the food processing, packaging, agriculture, and medical industries. The patent pending design contains a 303 stainless steel shaft collar, enclosed with a male and female shroud made from FDA compliant materials, and three O-rings with NSF compliant lubrication.
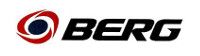
Since 1967, W.M. Berg has consistently set the standard of excellence as the world’s leading provider of miniature precision mechanical components. Started as a privately-held family business, Berg is now part of Rexnord Industries, a world leader in controls and automation.
These couplings are a class of coupling called Information Transmitting Couplings - These zero backlash, high torsional rigidity couplings are for precision positioning applications where constant velocity is required for accurate feedback control.
Bellows are a class of coupling called Information Transmitting Couplings - These zero backlash, high torsional rigidity couplings are for precision positioning applications where constant velocity is required for accurate feedback control.
A class of coupling called Shock Absorbing Couplings - As a result of flexible plastic members connecting their hubs, these couplings dampen vibrations and shock loads and electrically insulate shafting
A class of coupling called Shock Absorbing Couplings - As a result of flexible plastic members connecting their hubs, these couplings dampen vibrations and shock loads and electrically insulate shafting.
A class of coupling called Misalignment Couplings - The sliding center elements of these couplings compensate for lateral and angular misalignment caused by tolerance buildup or as a result of mounting.
A class of coupling called High Misalignment Couplings - These couplings allow the designer to have shafts that are intentionally offset, laterally or angularly, by a large amount.
A class of coupling called Information Transmitting Couplings - These zero backlash, high torsional rigidity couplings are for precision positioning applications where constant velocity is required for accurate feedback control.
A class of coupling called Information Transmitting Couplings - These zero backlash, high torsional rigidity couplings are for precision positioning applications where constant velocity is required for accurate feedback control.
A class of coupling called Shock Absorbing Couplings - As a result of flexible plastic members connecting their hubs,these couplings dampen vibrations and shock loads and electrically insulate shafting.
A class of coupling called Misalignment Couplings - The sliding center elements of these couplings compensate for lateral and angular misalignment caused by tolerance buildup or as a result of mounting.
A class of coupling called Misalignment Couplings - The sliding center elements of these couplings compensate for lateral and angular misalignment caused by tolerance buildup or as a result of mounting.
A class of coupling called High Misalignment Couplings - These couplings allow the designer to have shafts that are intentionally offset, laterally or angularly, by a large amount.